Adapting to Global Market Shifts: Manufacturing Strategies for 2025 and Beyond
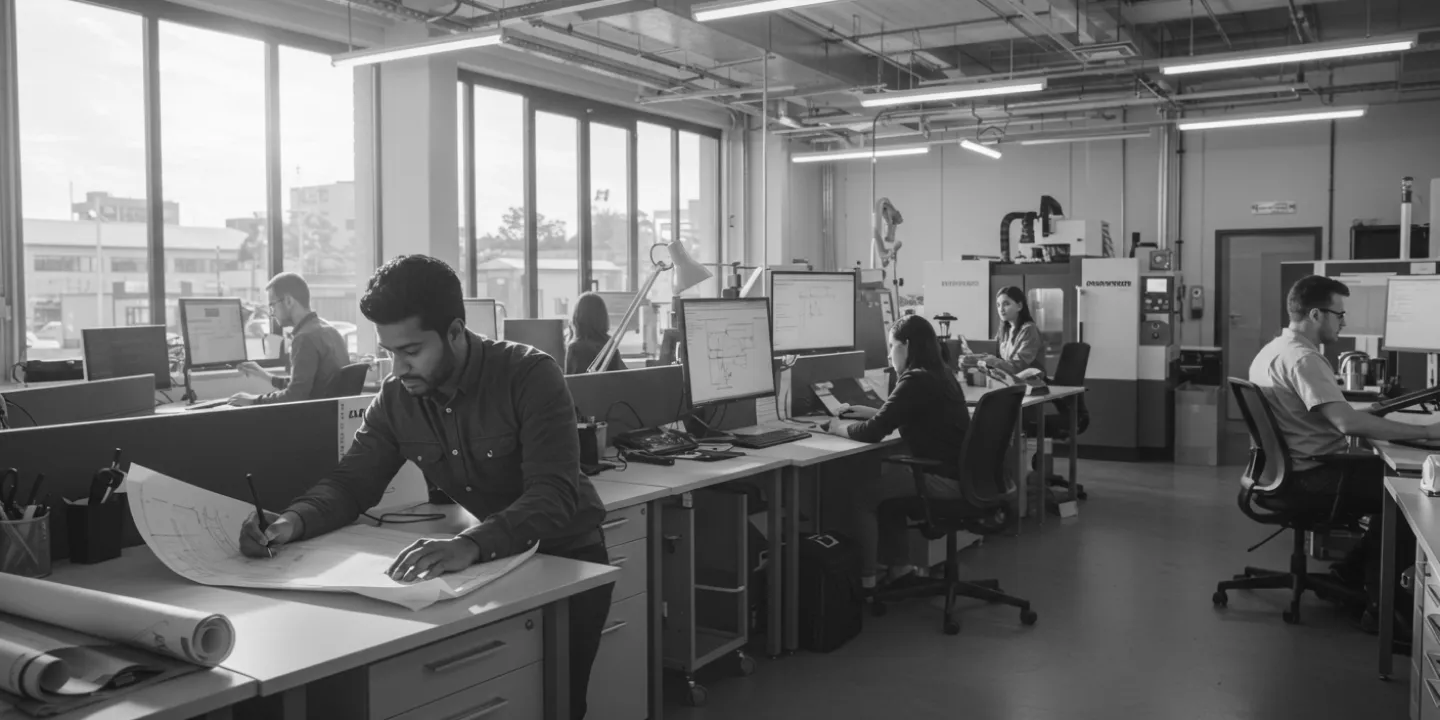
Global manufacturing is at a tipping point. The past five years have tested the sector's resilience as it continues to deal with industry-changing issues as varied as supply chain disruptions, geopolitical realignments, and the redrawing of trade routes and labor flows. Manufacturers are under pressure to not only maintain continuity, but also to adapt faster than ever before. The challenges are layered and they now include intensifying regulation, talent shortages, localized labor law complexities, and pressure to meet ESG commitments across jurisdictions. This isn’t business as usual. It’s a call to reimagine global operations with foresight, flexibility, and discipline.
The shifting terrain of global manufacturing
According to Deloitte’s 2025 Manufacturing Industry Outlook, 76% of manufacturers are concerned about rising geopolitical uncertainty and its impact on cross-border operations. Much of this uncertainty comes from changes to manufacturing laws and regulations around the world. The following countries provide some examples.
- Germany now has stricter co-determination laws that are increasing oversight around foreign-owned industrial operations, forcing manufacturers to engage more transparently with labor councils.
- Brazil has updated its health and safety framework and now requires enhanced psychosocial risk assessments across manufacturing environments — highlighting the expanding scope of employer liability.
- Vietnam continues to attract foreign direct investment (FDI) in electronics and industrial goods, but newly implemented labor classifications and benefit contribution rules are slowing hiring cycles and increasing compliance friction.
- India has consolidated its labor codes, and though this was designed to streamline processes, it has created fresh challenges as states implement their own variations.
- The UAE has new Emiratization targets that are shifting workforce composition requirements for the private sector, with penalties looming for those not compliant by mid-2025.
While many of these laws have had positive impacts for workers, it can be hard for global businesses to ensure full compliance with new and updated requirements, putting them at risk.
Emerging growth opportunities
Growth has not stalled, it has shifted. For instance, Poland saw a 9% YoY increase in FDI within the electronics and precision machinery sectors thanks to talent availability and access to EU markets. Mexico, meanwhile, is a top nearshoring destination for US-based manufacturers. However, companies looking to take advantage of shifting opportunities face delays due to complex entity formation timelines and confusion over updated classification laws. The Fictiv 2025 State of Manufacturing & Supply Chain Report found that 38% of manufacturers rank “speed-to-hire in new countries” as a top barrier to scaling global operations. These challenges underscore the importance of agility not only in supply chain logistics but also in workforce mobilization. Manufacturers who integrate HR compliance strategy with production planning are better equipped to capitalize on growth markets.
Strategic considerations for manufacturers in 2025
As highlighted in NTT DATA’s Manufacturing Trends 2025, smart factory implementation is accelerating. Yet, without the ability to secure skilled labor in new regions, investments stall. Executives and operations leaders should be asking:
- How exposed are we to misclassification risk in key production hubs like China, Brazil, and Germany?
- Are we capitalizing on emerging corridors like Poland or Vietnam, or avoiding them due to local employment law complexity?
- Have we updated contractor policies in LATAM and APAC in response to evolving benefit and tax contribution rules?
- Is our HR infrastructure flexible enough to support operational shifts driven by automation and digital transformation?
The EOR imperative: Simplifying the complex
At the end of the day, global growth isn’t just about capital investment or site selection. It’s also about people. The workforce is both the engine and the constraint. An employer of record (EOR) partner like Safeguard Global helps manufacturers turn workforce complexity into a strategic advantage. This is accomplished by enabling compliant, rapid hiring in nearly 190 countries without the burden of setting up local entities or mastering every nuance of local labor law.
With Safeguard Global, companies can onboard engineers in Poland, field technicians in Brazil, or QA teams in Vietnam — any kind of team, anywhere in the world. All of this happens while maintaining full compliance, cost predictability, and operational speed.
As the 2025 manufacturing map is redrawn by technology, regulation, and talent migration, agility and compliance are no longer reactive measures — they’re foundational strategy pillars. The most competitive manufacturers will be those who embed global workforce adaptability into their operating model.
Is your workforce strategy built for what’s next? Let’s talk about how Safeguard Global can help you seize the opportunity.
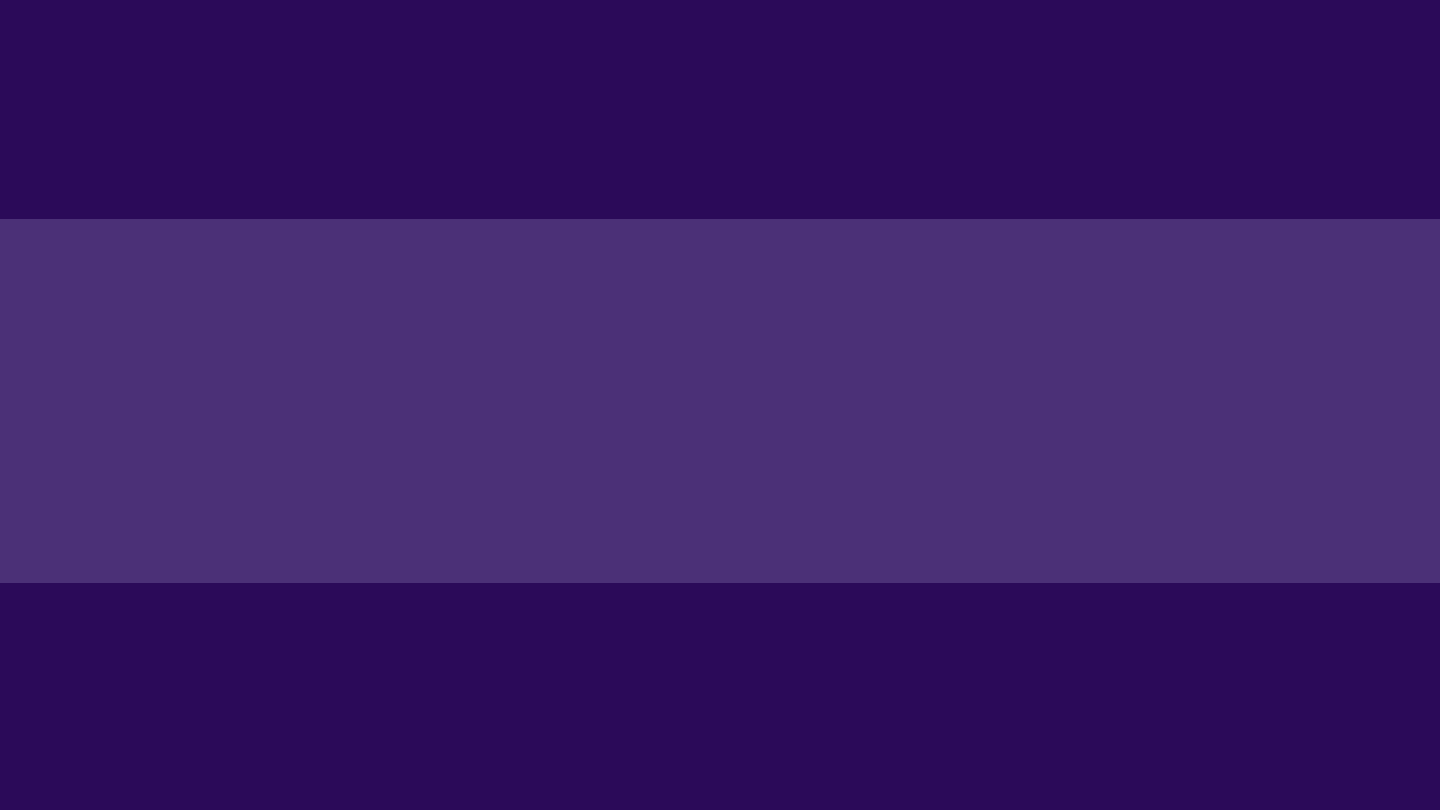
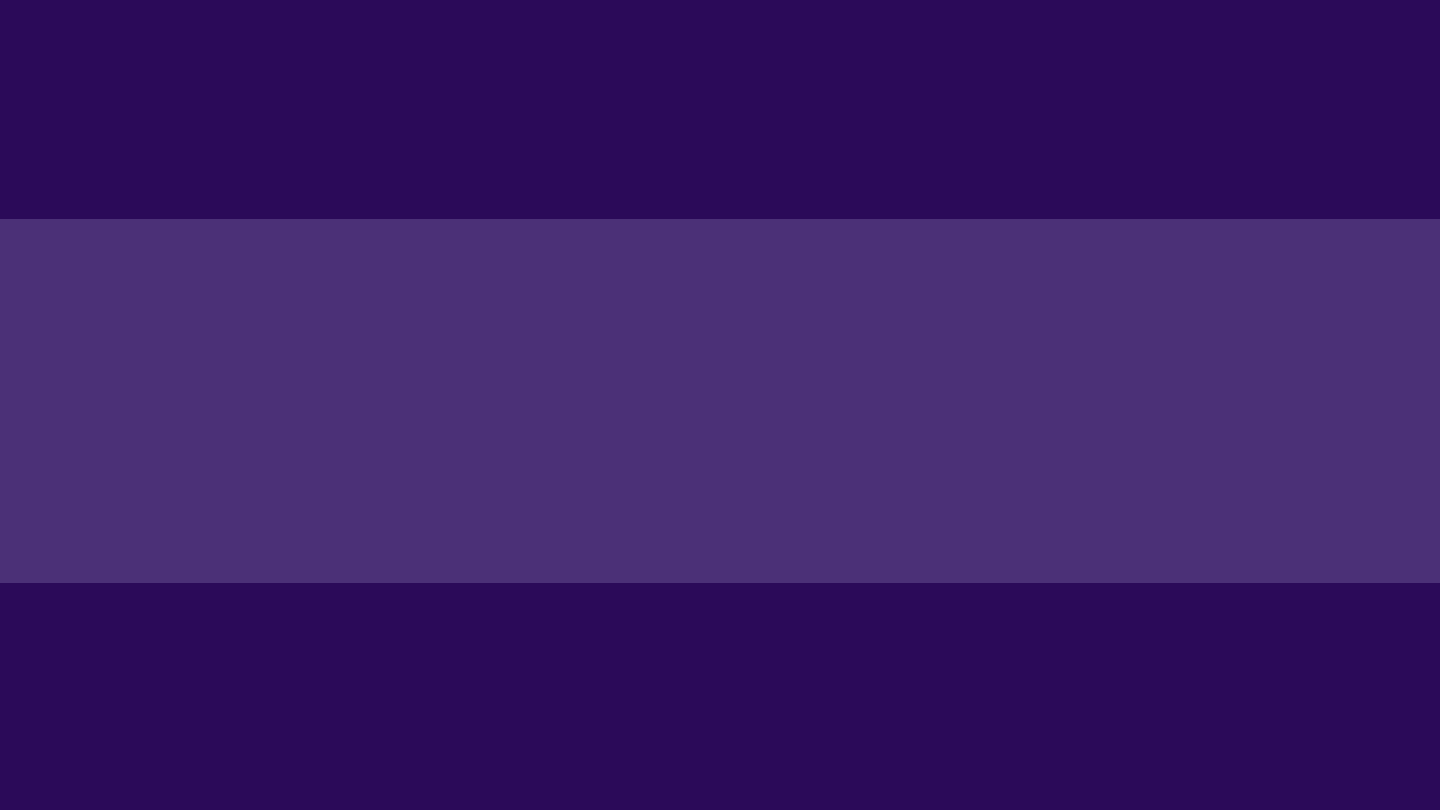
Contact Us
Book a demo today
Schedule an appointment